Unique Tips About Why Are HT Motors Connected In Star

How To Connect A 3 Phase Motor In Star And Delta Connection?
Unraveling the Star Connection
1. The Basics of High Tension (HT) Motors
Ever wondered why those hefty, high-tension (HT) motors in industrial settings are often wired up in a star configuration? It's not just a random choice; there's some serious electrical engineering logic behind it! Think of it like choosing the right tool for the job. You wouldn't use a hammer to screw in a bolt, right? Similarly, the star connection is perfectly suited for the unique demands of HT motors.—it's all about managing voltage and current effectively.
HT motors, as the name suggests, operate at high voltages, typically above 1000 volts. This higher voltage is necessary to deliver the considerable power needed for heavy-duty applications, such as driving large pumps, compressors, or mills. Because of these higher voltage, we need to handle it properly with a proper configuration. Dealing with such potent electrical energy requires careful consideration of insulation, safety, and, most importantly, how the motor is connected to the power supply.
The star (or wye) connection is one method of wiring three-phase electrical loads. In this configuration, one end of each of the three windings is connected to a common point, often called the neutral point or star point. The other ends of the windings are connected to the three-phase power supply. This arrangement provides several key advantages, making it a popular choice for HT motors.
So, why not just wire everything in delta? Well, hold your horses! The delta connection has its own set of applications, but it's not always the best fit for HT motors. The star connection offers some unique benefits that make it a more suitable choice in many scenarios, which we'll delve into soon.
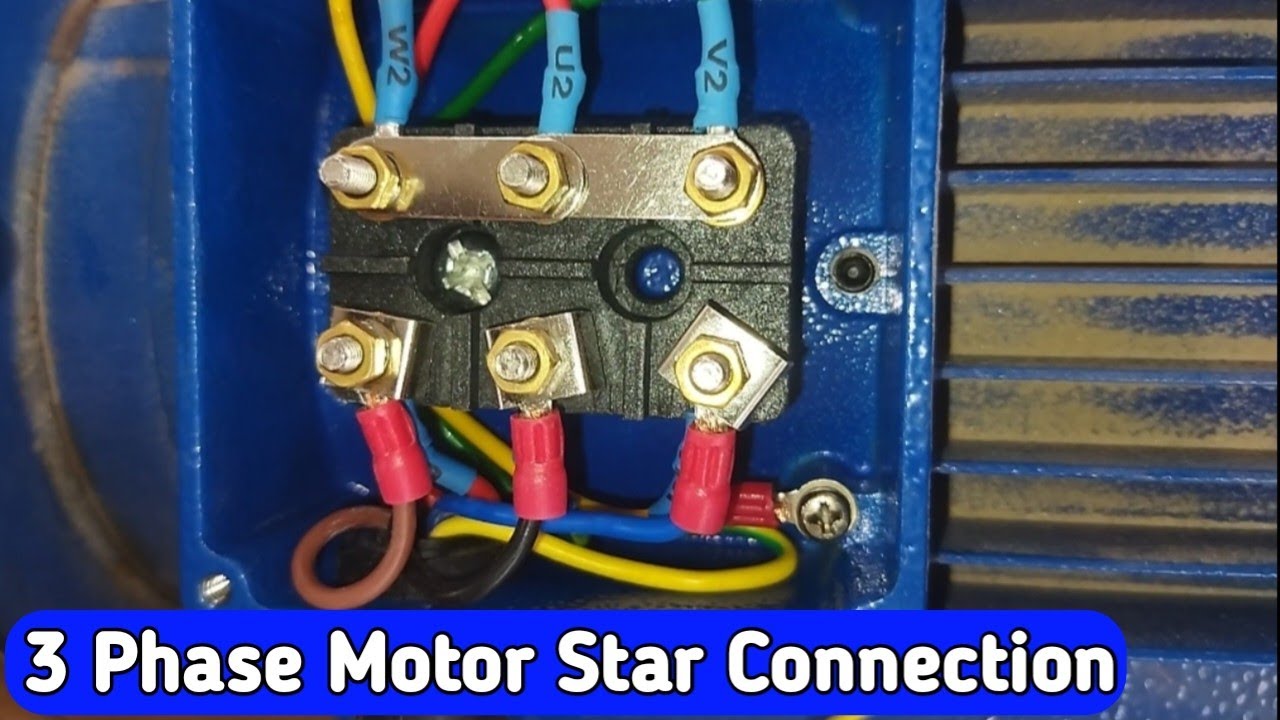
How To Proper Star Connection 3 Phase Motor
The Star Advantage
2. Sizing Up the Voltage Situation
One of the primary reasons for using a star connection in HT motors is voltage reduction. In a star connection, the voltage across each winding (the phase voltage) is lower than the line voltage (the voltage between any two lines of the power supply). Specifically, the phase voltage is equal to the line voltage divided by the square root of 3 (approximately 1.732). This seemingly simple mathematical relationship has significant implications for the design and operation of HT motors. I mean, who doesn't love a little voltage control?
By reducing the voltage across each winding, the star connection helps to alleviate stress on the motor's insulation. Higher voltages can lead to insulation breakdown, which can result in short circuits, equipment failure, and even safety hazards. Lowering the voltage, even by a factor of 1.732, can significantly extend the lifespan of the motor and reduce the risk of insulation-related problems. Think of it as giving your motor's insulation a little extra breathing room.
Furthermore, the reduced voltage also helps to limit the inrush current during motor startup. When an electric motor is first switched on, it draws a large surge of current, known as the inrush current. This inrush current can be several times higher than the motor's normal operating current, potentially causing voltage dips, overheating, and even damage to the motor or the power supply. The star connection mitigates this issue by reducing the initial voltage applied to the windings, thereby limiting the inrush current and preventing potential problems.
Essentially, the star connection is like a voltage "soft start" mechanism built right into the wiring. It helps to protect the motor from overvoltage and overcurrent stresses, ensuring more reliable and efficient operation. It is important to mention that the exact values of the current and voltage will depend on the motor rating and the grid specifications. But you will find that the star connection plays a huge role in providing you with the above mentioned advantages in handling HT motors.
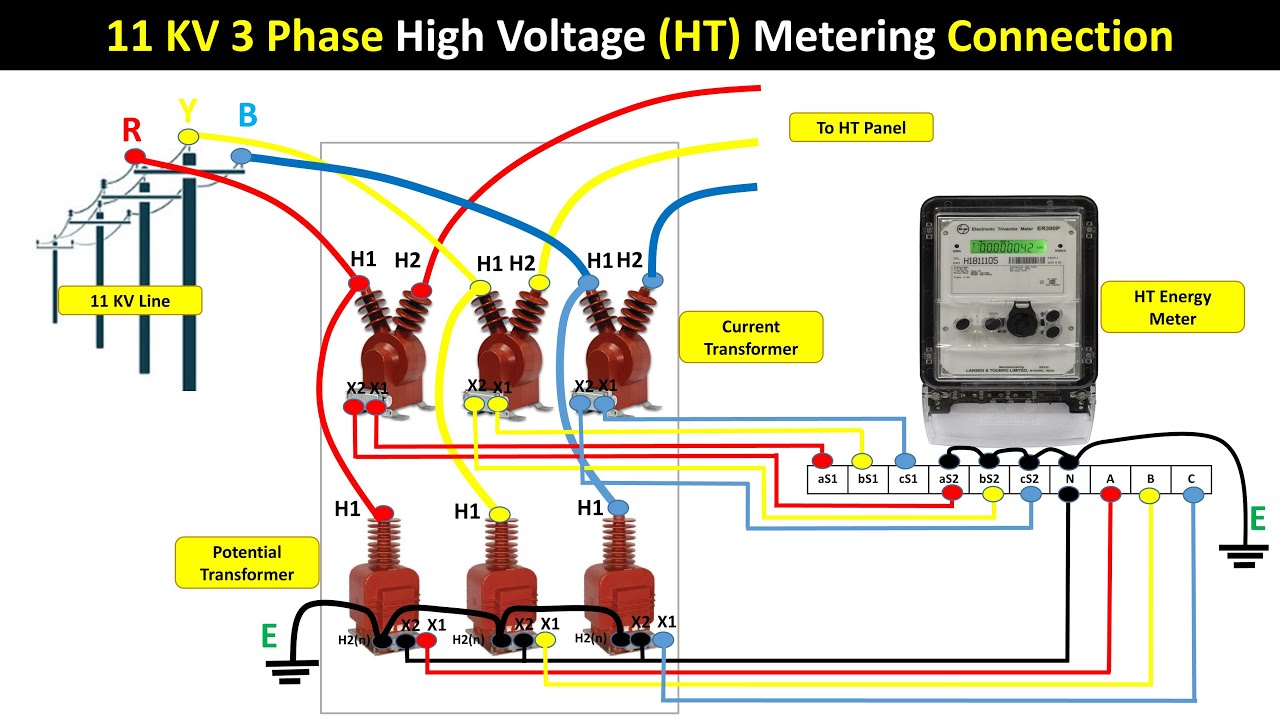
11KV High Voltage HT Metering Connection With CT & PT YouTube
Inrush Current Control
3. Why Inrush Current Matters
We've touched upon inrush current, but let's dive a bit deeper into why it's such a concern, particularly for HT motors. Remember, HT motors are often used to drive heavy loads, which means they require a significant amount of starting torque. The initial demand for current can be substantial, and without proper management, it can wreak havoc on the electrical system.
Imagine a scenario where you switch on a large HT motor directly, without any form of inrush current control. The sudden surge of current can cause a dip in the overall voltage of the electrical grid. This voltage dip can affect other equipment connected to the same grid, potentially leading to malfunctions or even shutdowns. In industrial settings, where numerous machines and processes are interconnected, such disruptions can have significant economic consequences.
Moreover, the high inrush current can also generate excessive heat in the motor windings, potentially damaging the insulation and shortening the motor's lifespan. Repeated exposure to high inrush currents can lead to cumulative damage, eventually resulting in motor failure. Preventing this damage is a top priority in HT motor applications, and the star connection plays a crucial role in achieving this.
By limiting the inrush current, the star connection helps to ensure a smoother and more controlled startup. This not only protects the motor itself but also minimizes the impact on the surrounding electrical infrastructure. It's a win-win situation, where both the motor and the power supply benefit from the reduced stress.
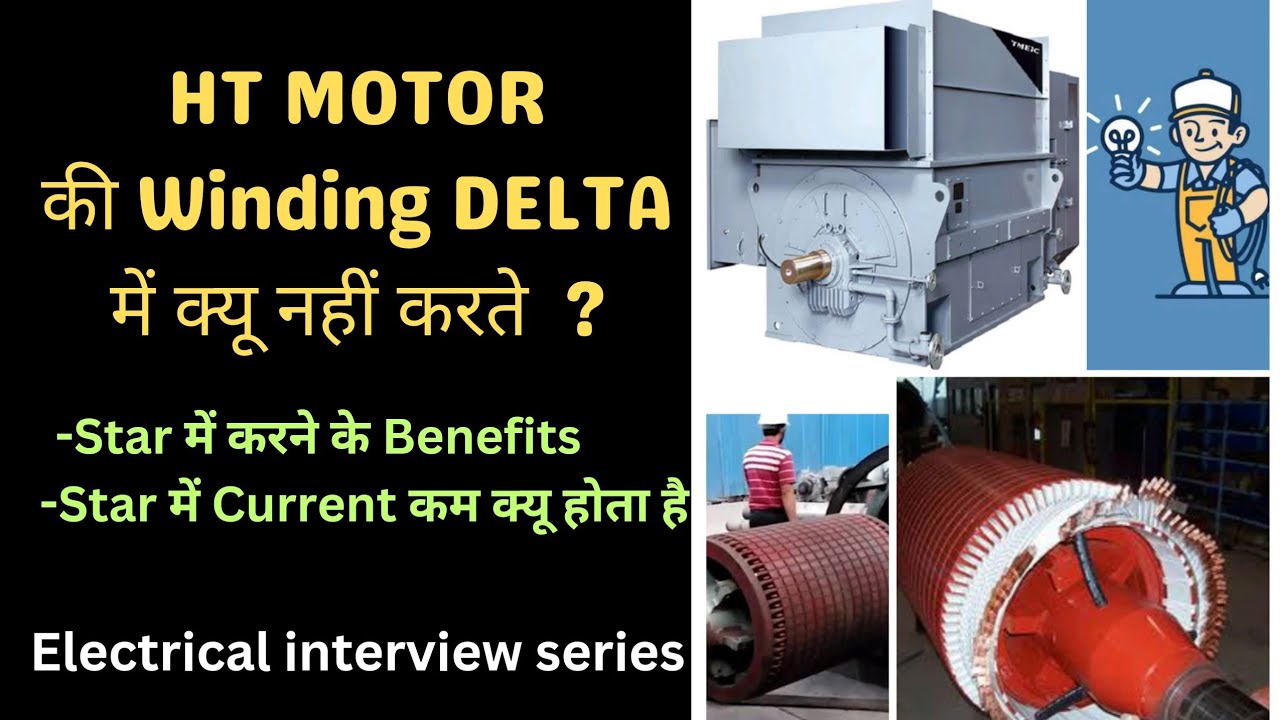
Why HT Motors Are Not Connected In Delta Benefits Star
Neutral Grounding
4. The Importance of a Grounded Neutral
Another key aspect of the star connection in HT motors is the availability of a neutral point. This neutral point can be grounded, providing a reference point for the electrical system and enhancing safety. Grounding the neutral point helps to prevent voltage imbalances and provides a path for fault currents to flow back to the source in the event of a ground fault.
When a ground fault occurs, a live conductor accidentally comes into contact with the ground or a grounded object. This can create a hazardous situation, as the fault current can flow through unintended paths, potentially causing electric shock or fire. A properly grounded neutral point provides a low-impedance path for the fault current, allowing it to quickly trip a circuit breaker or fuse and isolate the faulty circuit.
Furthermore, grounding the neutral point helps to stabilize the voltage levels in the system. In an ungrounded system, voltage imbalances can occur due to variations in load or other factors. These voltage imbalances can lead to erratic motor operation, increased stress on the windings, and even premature failure. Grounding the neutral point helps to maintain a more stable and balanced voltage distribution, ensuring more reliable and efficient motor performance. Consider it like having a reliable anchor for your electrical system, keeping everything stable and secure.
The grounded neutral point also facilitates the use of protective devices, such as ground fault relays. These relays are designed to detect even small ground fault currents and quickly trip the circuit breaker, preventing further damage and protecting personnel. Ground fault protection is an essential safety feature in HT motor applications, and the grounded neutral point provided by the star connection is crucial for its effective implementation. So, it isn't just about reducing current, its also about safety in the long run!

Star Delta Connection On Motor
Star-Delta Starting
5. Combining the Best of Both Worlds
While the star connection offers several advantages for HT motor operation, it's worth noting that a technique called star-delta starting is often employed. This method combines the benefits of both the star and delta connections to achieve optimal starting and running performance. Star-delta starting involves initially connecting the motor windings in a star configuration during startup, and then switching to a delta configuration once the motor has reached a certain speed.
As we've discussed, the star connection reduces the voltage applied to the motor windings during startup, limiting the inrush current and preventing potential problems. Once the motor has gained momentum and the inrush current has subsided, the windings are switched to a delta configuration. In the delta connection, the full line voltage is applied to each winding, allowing the motor to deliver its full rated torque and power.
The star-delta starting method provides a "soft start" for the motor, minimizing the stress on the electrical system and the motor itself. It's a particularly useful technique for HT motors that drive heavy loads, as it allows the motor to gradually build up speed without causing excessive voltage dips or overheating. The process uses a timer to switch between both modes, hence it is important to set the timing correctly.
In essence, star-delta starting offers a compromise between the reduced inrush current of the star connection and the full torque capability of the delta connection. It's a clever way to optimize motor performance and protect the electrical system, making it a common practice in many HT motor applications.