Ideal Tips About What Is The Difference Between Cogs And BOM

Everything You Need To Know About COGM Vs COGS The Megaventory Blog
Unraveling the Mystery
1. COGS and BOM
Ever wondered what separates the Cost of Goods Sold (COGS) from a Bill of Materials (BOM)? They both play crucial roles in understanding a product's value, especially in the world of manufacturing and retail. Think of them as two peas in a pod, intimately linked but serving distinct purposes. It's a bit like comparing your grocery bill to the actual recipe you used to cook dinner. Both relate to the food, but one shows what you paid, and the other details what went into it.
The Bill of Materials (BOM) is essentially a detailed recipe card for a product. It meticulously lists all the raw materials, components, sub-assemblies, and even the quantities of each, required to manufacture a single unit of the finished product. Imagine building a Lego set; the BOM is that instruction manual showing every brick needed. It doesn't tell you how much those bricks cost, just what bricks you need.
Now, COGS, or Cost of Goods Sold, is the total expense directly attributable to producing the goods a company sells. It includes the cost of the raw materials (the bricks from our Lego analogy, and their prices), direct labor (the cost of the people assembling the bricks), and any direct manufacturing overhead (like the electricity used in the factory where the bricks were made — although attributing that precisely is another story!). COGS appears on the income statement and directly impacts a company's profitability.
So, while the BOM is a list, COGS is a dollar figure. The BOM informs the COGS, but it's not the COGS itself. Confused yet? Don't worry, we'll break it down further. Think of it like this: your BOM is the ingredients list for a cake, while your COGS is the total amount you spent at the grocery store to buy those ingredients.
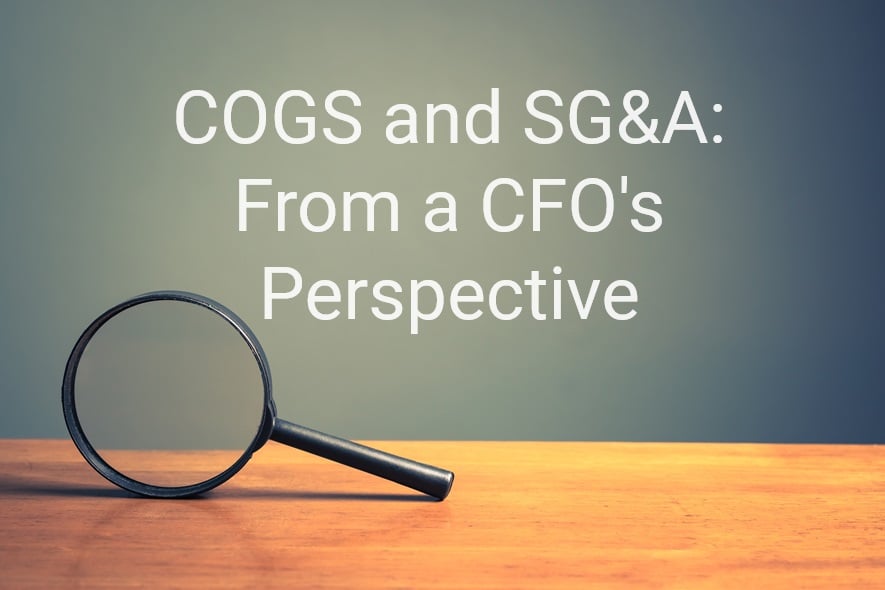
Diving Deeper
2. What's in a BOM? More Than Just a List
A BOM isn't just a haphazard list scrawled on a napkin; it's a structured and comprehensive document. A well-constructed BOM includes a part number for each item, a description (so you know exactly what you're dealing with), the quantity needed per finished product, the unit of measure (e.g., meters, kilograms, pieces), and sometimes even supplier information. Some BOMs also contain notes about specific assembly instructions or quality control procedures.
There are different types of BOMs, depending on their purpose. An engineering BOM (eBOM) is used during the design phase and focuses on the functional aspects of the product. A manufacturing BOM (mBOM) is used in production and emphasizes the parts and components needed for assembly. And a sales BOM (sBOM) describes the product as sold to the customer, which might include optional accessories or bundled items. Think of them as variations on a theme, each tailored to a specific audience.
Effective BOM management is crucial for efficient manufacturing. A poorly managed BOM can lead to errors, delays, and increased costs. Imagine ordering the wrong Lego bricks and halting the entire assembly line! BOM management software helps companies keep track of changes, revisions, and different versions of the BOM, ensuring that everyone is working with the most up-to-date information. It also helps manage supplier data and pricing information for more accurate cost calculations.
A BOM can even include things like adhesives, paints, or even the packaging material. It's all about capturing everything that goes directly into creating the finished product. Without a solid BOM, it's nearly impossible to accurately calculate your COGS and, therefore, properly price your product. Its the foundation upon which all other cost analyses are built.
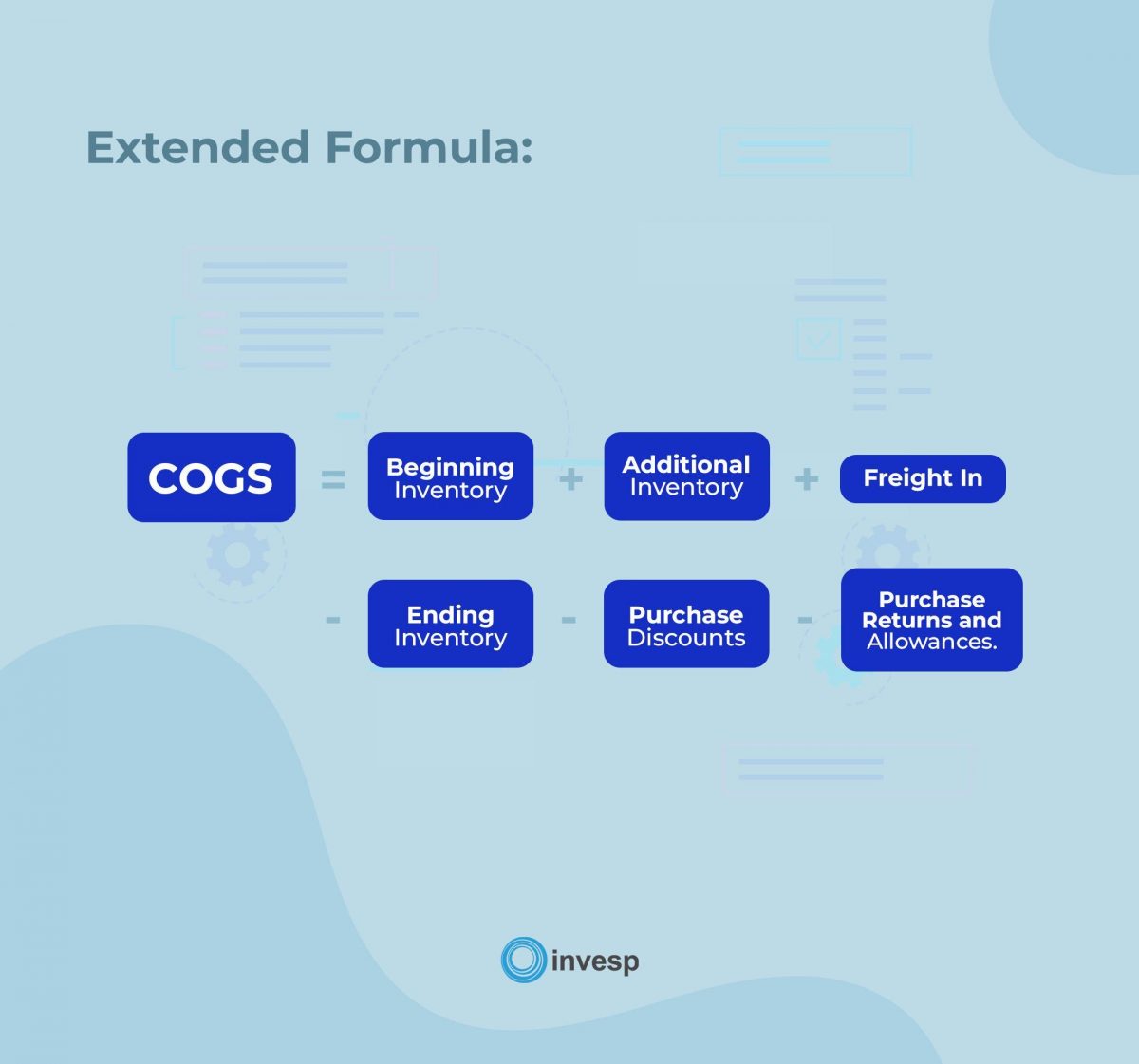
COGS Formula 101 Essential Insights For Entrepreneurs
The Power of COGS
3. COGS
Calculating COGS isn't just about adding up the cost of the raw materials. It also includes direct labor costs — the wages and benefits paid to the workers directly involved in the manufacturing process. This could include assembly line workers, machinists, or even quality control inspectors. Accurately tracking direct labor is essential for understanding the true cost of production.
Another component of COGS is direct manufacturing overhead. This includes costs like factory rent, utilities (electricity, water, gas), depreciation of manufacturing equipment, and even the cost of factory supplies (cleaning supplies, lubricants, etc.). These costs are directly related to the manufacturing process but are not easily attributable to a specific product. Overhead is often allocated to products based on a pre-determined rate, such as machine hours or direct labor hours.
Accurate COGS calculation is vital for several reasons. First, it allows companies to determine the profitability of their products. By subtracting COGS from revenue, companies can calculate their gross profit, which is a key indicator of financial performance. Second, COGS is used to value inventory. Inventory is typically valued at cost, and COGS provides the basis for this valuation. Third, COGS is used for tax purposes. Companies are required to report their COGS on their income tax returns, and an accurate calculation can help minimize their tax liability.
COGS can fluctuate based on various factors. Changes in raw material prices, labor rates, or manufacturing overhead can all impact COGS. For example, a sudden increase in the price of steel would directly increase the COGS of products that use steel. Companies need to monitor these factors closely and adjust their pricing or production strategies accordingly. Think of it as constantly recalibrating your business GPS to stay on the most profitable route.

What Is The Difference Between COGS Vs. Operating Expenses Small
COGS vs. BOM
4. Distilling the Essence
The fundamental difference lies in their nature: The BOM is a list of materials, while COGS is a financial calculation. The BOM focuses on what goes into the product, while COGS focuses on how much it costs to produce it. One is a blueprint, the other is a budget.
Think of the BOM as a recipe and COGS as the cost of all the ingredients for that recipe. If you change the recipe (modify the BOM), you will likely change the cost of ingredients (impact the COGS). They are interdependent.
While both COGS and BOM are essential for effective business management, COGS is of particular interest to the accounting and finance departments and external stakeholders such as investors and analysts. BOM on the other hand, tends to be the realm of engineering, manufacturing, and supply chain management teams.
Ultimately, understanding the interplay between COGS and BOM is crucial for making informed business decisions. By carefully managing your BOM, you can control your raw material costs and improve your overall COGS. And by accurately calculating your COGS, you can determine the profitability of your products and make better pricing and production decisions. It's all about having a clear picture of your entire manufacturing process, from the initial design to the final sale. And maybe, just maybe, making a bit of money along the way.

Practical Applications
5. Real-World Examples
Let's imagine a small furniture manufacturer that produces wooden chairs. Their BOM would list all the components needed to build one chair: wood (measured in board feet), screws, glue, varnish, and fabric for the seat. The COGS would include the cost of the wood, screws, glue, varnish, and fabric, plus the wages paid to the carpenters who assembled the chair and the cost of operating the woodworking equipment.
Now, let's say the manufacturer decides to switch to a cheaper type of wood. This change would directly impact the BOM (a new type of wood is listed) and the COGS (the cost of wood decreases). The manufacturer can then use this information to adjust their pricing strategy, potentially increasing their profit margin or offering a more competitive price.
Conversely, let's say the price of varnish increases significantly. This would not affect the BOM (the type and quantity of varnish remain the same), but it would increase the COGS. The manufacturer would need to reassess their pricing to account for the higher cost of varnish, possibly passing the cost on to the customer or finding a cheaper alternative varnish (which would then affect the BOM!).
Businesses can optimize their profitability by using BOM and COGS analysis to identify cost savings opportunities. Perhaps a more efficient manufacturing process can reduce labor costs (affecting COGS), or a supplier offering better prices on raw materials can be found (affecting both BOM and COGS). The key is to continuously monitor both the BOM and COGS and look for ways to improve efficiency and reduce costs. Its a never-ending quest for better margins!

Frequently Asked Questions (FAQs)
6. Your Burning Questions, Answered!
Q: Is labor always included in COGS?A: Only direct labor is included in COGS. Direct labor refers to the wages and benefits paid to workers who are directly involved in the production process. Indirect labor, such as the salaries of factory supervisors or maintenance personnel, is typically classified as overhead and allocated to COGS.
Q: Can COGS be negative?A: No, COGS cannot be negative. COGS represents the cost of producing goods that have been sold. Costs are always positive values. However, your profit margin could become negative if your COGS exceeds your revenue!
Q: How often should I update my BOM and COGS?A: The frequency of updates depends on the nature of your business and the volatility of your input costs. Businesses with rapidly changing product designs or fluctuating raw material prices should update their BOM and COGS more frequently — perhaps monthly or even weekly. Businesses with more stable operations may only need to update their BOM and COGS quarterly or annually. The important thing is to stay on top of changes that could significantly impact your profitability.